Introduction
Circular Economy (CE) is identified as one of the greatest viable approaches to sustainability. It is a new paradigm that considers how to design with the intention to reduce, reuse and recycle construction materials as much as possible. It also means designing for durability to keep products, materials, and components circulating in the economy, favoring activities that conserve values in the form of energy, materials, and labour. The objective of circular economy requires influencing the behaviors of stakeholders in the construction supply chain, with the aim of keeping materials out of the waste stream. Additionally, this philosophy seeks to influence the design and construction of buildings to reduce carbon footprint effectively.
Circular economy concept can be traced to many origins, but there is no clear evidence of a single origination. However, the literature demonstrates that CE is mainly originated in environmental economics, industrial ecology eco-industrial development (EID) theory. Although the application of CE concept varies from one region to another, however, in North America, CE is applied to enhance the principle of reduce, reuse, and recycle (3Rās) toward achieving sustainable and responsible consumption and production patterns, where reducing is the act of being aware of consumption habits by consuming fewer resources, and avoiding unnecessary waste; reusing, on the other side, involves finding new purposes for old products or repurposing items instead of discarding them; whereas recycling consists of processing waste materials to create new materials. These three Rās have significant environmental benefits as they help to conserve natural resources, reduce landfill waste, and decrease pollution. Hence, the practical idea of CE systems is to ensure that added value in the material is kept within the economic circle for as long as possible to avoid the generated waste being piled into landfills.
Despite of the growing interest and knowledge about CE, recent studies in that area, show no evidence that they explicitly target the AEC industry due to their complex nature and lack of a general acceptance of the characterization and orientation, which is resulting in a low recognition rate, especially for new building projects. Conventional buildings are another significant barrier that hinders the application of CE in the AEC industry due to their monolithic nature, architectural characteristics, lack of standardization and measurements, and underdeveloped closed-loop stakeholders in the design and building method. Furthermore, the AEC industryās linear structure (i.e., take-make-waste) makes it one of the largest consumers of energy and raw materials, which negatively affect the environment through its contribution to greenhouse gas emissions and waste generation.
However, presently, the design of buildings is becoming more innovative and increasingly focuses on the principles of sustainability and circular economy, with a specific emphasis on reducing waste and environmental impact. The methods used to achieve the associated sustainability benefits are modular prefabrication and 3D concrete printing construction of buildings. Modular construction is known as one of the primary sustainable off-site construction methods in the recent past, with a significant potential to improve performance and productivity in the construction industry, which would solve the industryās existing challenges through the reuse of building components. Another emerging technology in construction is 3D concrete printing, which offers increased design flexibility and reduction in the use of material. It is seen as the future of construction as it provides solutions for sustainability, resource-efficient practices, and design innovation.
On another side, integrating BIM and circular economy is becoming an innovative advancement to moving construction activities toward sustainable options that support a greener, cleaner, and more competitive economy by infusing value into products throughout their life cycle. For example, tools such as geo-design and geolocation embedded in a web based map services provide paths that promote CE strategies for design and waste management through the various analyses of CDW from generation, sorting, collection, transportation, and recycling. Building Information Modeling (BIM) is promoted as an enabler of innovation in the design and construction of projects due to its information abilities, data management capabilities, and interdisciplinary work opportunities. It also plays a significant role in building design, enabling architects and engineers to create detailed digital models of buildings and their surroundings. The technology integrates and manages all projectsā information over their lifecycle, including planning, design, estimating, construction, operation, and end-of-life of a building facility . Ultimately, integrating circular economy, modular and 3D concrete printing design, along with BIM and geolocation technologies can create a powerful tool for attaining sustainable and environmental friendly buildings. However, until present, studies related to quantifying the circular economy conceptto enhance the sustainability of building construction, such as indicators, frameworks, or models are not entirely ascertained in the AEC industry. Therefore, this paper proposes the development of a model that integrates BIM and the concept of circular economy to enhance the sustainability of construction in order to minimize the lifecycle waste that is generated out of various construction methods (i.e., conventional, modular, and 3D concrete printing) at the conceptual design stage of buildings. The methodology of the proposed model is implemented based on the design for deconstruction (DfD), prefabrication technologies and modularization, selective deconstruction, and demolition phases. The proposed model will have the capability to quantify the wasted material, select the equipment needed for handling the waste and estimate the related costs associated with loading and hauling the wasted materials at the various stages of a project based on the adopted construction method.
Literature Review
Leising et al. defined Circular Economy (CE) as a lifecycle approach that optimizes the buildingsā useful life, integrates the end-of-life phase in the design stage and uses new ownership models to temporarily store materials in a building that acts as a building material bank. CE also uses practices in all phases of a buildingās life cycle to keep the materials longer in a closed loop to reduce the use of new natural resources in the construction of building projects . Adams et al. stressed that the application of CE by the construction industry is mainly limited to minimizing the construction waste and recycling. Xue et al. considered CE as an appropriate approach to managing construction waste by reusing products. Sanchez and Haas recognized adaptive reuse of buildingsā materials as attractive for their restorative and regenerative nature, aligning with CE building principles. Minunno et al. explored the environmental benefits of a building by using three CE practices: 1) design for disassembly (DfD) to enable componentsā second life; 2) integration of reused materials at the construction stage; and 3) implementation of adaptable design to eliminate waste during the operation stage. However, most scholars focused on ādesign for deconstructionā (DfD) as a critical solution to facilitate material reuse in building construction, although the potential carbon benefits of reusing construction materials are not immediately gained . Pomponi and Moncaster listed the following six dimensions: government; economic; environment; behavior; society; and technology, as drivers and barriers to adopting CE by conceptualizing the AEC industry at the material and component, building unit, and city levels. While, added seven weighted dimensions, listed as: energy; materials; water; and 3Rs (reduce, reuse, and recycle) for the scale of resource management; waste and emissions for environmental impact; and CE principles. However, the shared principles of CE reside in adequate resource management and waste minimization by closing material and energy loops . Thus, waste from construction activities can be reusable through the closing resourceās loops of the CE principle known as recycling. Recycling is classified into upcycling and downcycling. Upcycling is considered a process where used materials are converted into products of the same or higher value in their second lifecycle . While downcycles are recycling processes done in a way that the resulting product value is lower than the original product. However, recycling is only effective when producers of construction and deconstruction waste find it cheaper than sending waste to landfill site; when users of construction aggregates find recycled aggregates more affordable than similar quality newly quarried aggregates . However, noted that when directly comparing emissions of upcycling with linear landfilling for construction materials, consideration for other essential aspects of the process, such as transport to treatment facilities or energy consumed in demolition versus deconstruction, should be made. Hence, several studies have shown that innovative upcycling materials have resulted in less environmental impact than virgin materials.
According to , the linear project life cycle approach focuses on the new construction of high-efficient and eco-friendly buildings, while circular building principles shift the thinking in the perception of holistic sustainability in construction by switching from the traditional creative and innovative to a restorative and regenerative approach. The study argued that project planning must shift from a linear to a circular economy and proposed a closed-loop cycle approach with distinct stages, decision gates, definition categories, and planning methods, such as selective disassembly, LCA monetization protocols and optimization methods. López Ruiz et al. identified relevant strategies for adopting a CE model to tackle the construction and demolition waste sector in five life cycle stages listed as pre-construction; construction reconstruction; collection and distribution; end-of-life; material recovery and reproduction. Guerra et al. summarized waste reduction strategies into the following five categories:1) design; 2) method of construction (prefabrication technologies, modularization); 3) use of effective waste management system; 4) government legislation; and 5) improvement in practitionersā attitudes. Adams et al. studied the CE aspects of construction waste minimization and recycling across a buildingās life cycle to develop key application aspects at various stages. They identified three main design strategies for CDW management as follows: i) design for waste prevention; ii) design for deconstruction; and iii) use of prefabricated elements. According to , CDW is generated as a result of the following reasons: i) design errors; ii) inadequate procurement and planning; iii) inefficient construction material handling; iv) residues of raw materials; and v) unexpected changes in building design.
Furthermore, construction and deconstruction site waste is a significant challenge for the AEC industry due to its voluminous nature and the associated environmental impacts. It is described as waste generated during a structureās projectās life cycle, especially during construction, renovation, or end-of-life . Waste generated from construction activities is ranging between 25 and 33% of Canadaās total solid waste, which is estimated to be around 10 million tons, while in the European Union countries, that value accounts for 36% (equivalent to 924 million tons), whereas in the United States it is close to 67% (corresponding to 34 million tons), and Chinaās percentage falls between 30 and 40% (amounting to a staggering 2360 million tons) . This means that the design stage strategically influences the generation of waste during the construction of projects. Notably, about 90% of relevant decisions related to the buildingās configuration, composition, process, and schedule are made during the conceptual design stage. Based on the above, it will be obvious that the design stage is the most effective way to integrate CDW reduction strategies into the building life cycle.
Recently, various studies promoted the design for deconstruction or design for disassembly (DfD) as a circular economy technique to facilitate a sustainable management of the waste life cycle at the design stage of buildings . DfD is a process where buildings are designed to facilitate adaptation, renovation, and reuse of materials and components at their end of life for material recovery, building relocation, component reuse, and material recycling or remanufacturing . Using prefabricated components or elements is closely associated with the implementation of DfD in the building construction, which can increase circularity in the AEC industry. The process involves moving the manufacturing of materials and components to an off-site location in a safe and controlled external environment; it is recognized as a vital solution to reduce the generation of waste during the project design and construction phases . Since elements are constructed off-site and assembled on-site, it promotes the interchangeability of the building components and offers flexibility, that aids the deconstruction of a project at the end of its life. The use of prefabricated systems and elements can reduce labor-intensive construction trades, reduce CDW by around 65% to 80%, and minimize various construction waste streams [.
Building Information Modeling (BIM) plays a significant role as a platform to create and store sophisticated 3D building models, including their schedule, cost estimate, analysis, and waste management with its associated commercial tools that support the design team to achieve design for deconstruction . Akinade et al. assessed the existing DfD tools and identified essential functionalities of a BIM-based tool for DfD. They identified seven functionalitiesā keys retrieved from focus group interviews: i) improved stakeholdersā collaboration; ii) visualization of deconstruction process; iii) identification of recoverable materials; iv) deconstruction plan development; v) performance analysis and simulation of end-of-life alternatives; vi) improved building whole life management; and vii) interoperability with existing BIM tools. Furthermore, BIM can integrate construction engineering information, process, and resources at various project life cycle phases and efficiently utilize all parties involved. Interest in BIM technology adoption for waste minimization is growing considerably . Won and Cheng, identified potential opportunities of BIM for efficient CDW management, such as design review and coordination, quantity takeoff, site utilization planning, construction, digital fabrication, and 3D control and planning. Liu et al. developed a BIM-aided CDW management framework that addresses the causes of design waste to assist architects make suitable decisions at the design phase of buildings. Won et al. studied the potential of using BIM tool to eliminate the major causes of CDWās generation by integrating the processes of building design and construction. A study by claimed that BIM could minimize CDW by enhancing the accuracy and quality of the design and construction data, thereby reducing design errors, rework, and unexpected changes. They developed a BIM-based system to improve the accuracy of managing demolition waste with a reconstructed 3D model. Likewise, proposed a BIM-based system that allows CE to effectively store the information of material and building components, accounting for recycling materials and reusable components. BIM can also facilitate data management in quantifying building components that can be reused and recycled beforehand as well as estimate the associated cost for waste disposal options the during construction and at the deconstruction phase for different construction methods of buildings. McNeil-Ayuk and Jrade proposed an integrated BIM and sustainable design model that selects those construction methods for further waste management by considering usersā interactions and input from conventional, modular and 3D concrete printing construction.
Google Maps services provide tools for route optimization, real-time tracking, data visualization, and decision support. The integrated technology provides a platform for several location-based services, which can be employed for decision-making. For instance, integrating BIM and Google Maps can optimize the reuse and recycling of waste to minimize the wasted materials, overall energy cost, demolition time and impacts on the surrounding environment during the demolition stage of a construction project when the most significant amounts of wasted materials are generated . Song et al. integrated BIM and web-based map system technologies, including information on supply and demand, transportation costs, and recovery prices of waste to select an adequate recycling facility. Furthermore, the capabilities of map services aid the analysis and optimization processes of waste distribution, such as delivery networks, transport services, and environmental assessment. Al-saggaf and Jrade integrated the desktop-based map transportation network with material information from BIM 3D model to estimate the waste sorting and the number of trucks required to load and haul demolition waste within an IFC environment.
However, according to a study commissioned for Environment Canada, only about 16% of CDW was reused or recycled (653,000 tons), while the remaining 84% was disposed (3,353,000 tons), mainly in landfills . However, highlighted that the amount of CDW generated depends on the construction method and the materialsā composition. For instance, prefabricated structures will generate less construction waste, as the in-factory manufacturing process is less wasteful and designs are specific for each building. The need to develop a CDW management plan to establish measures for waste reduction before, during, and after construction activities during the design phase was emphasized by . Esa et al. proposed a CE approach using site waste management plans for the construction and renovation of buildings. Whereas, considered designing and implementing site waste management plans (SWMP) are effective strategy for improving CDW.
Moreover, a comprehensive evaluation of the existing literature revealed that there are some existing waste management tools used to improve waste prediction and quantification, such as SMARTStart, SMARTAudit, True Cost of Waste Calculator, and smart waste developed by Building Research Establishment (BRE) SMARTWaste, Net Waste Tool (NWT), Designing out Waste Tool for Buildings (DoWT-B), and Web-based Construction Waste Estimation System (WCWES) . However, these tools are limited to regional projects and do not provide adequate quantification methodology. Therefore, they are neither compatible with BIM tools nor actively employed during the building design . Thus, this proposed study presents a straightforward methodology for developing and testing an integrated model for evaluating and planning the construction and deconstruction of waste.
The proposed model estimates the quantity of wasted materials based on the mass balance approach for the construction stage and the material commonly incorporated into a building for the end-of-life stage using BIM customized model(s) with various waste parameters. The integrated model automates the process of quantifying the wasted material at different lifecycle stages, identifies and calculates waste handling equipment and their productivity, and estimates the associated cost for loading and hauling the waste of a building project all within a BIM environment by integrating Google Maps, MySQL, and CE concept at the conceptual design of buildings.
Model Development Methodology
The integrated model will aid in quantifying the material waste, identifying the waste handling equipment, and the costs associated with loading and hauling wastes at the construction and end-of-life stages of building projects. The objective of the integrated model is to incorporate CDW management strategies during the conceptual design stage based on the principles of circular economy by using BIM tool (Autodesk Revit) and Google Maps to enhance the sustainability performance of buildings through three construction methods (conventional, modular, and 3D concrete printing). The development methodology for the integrated model entails a systematic automation approach to extend design and analysis tools via the development of a plug-in that seamlessly integrates with the conceptual design model to enhance its functionality, capabilities, and flexibility in a unified design environment. Achieving flexibility is a vital development requirement as it ensures that the model is versatile and reliable throughout its lifecycle, allowing designers to incorporate and revise data in a user-friendly manner. The development methodology starts by creating the modelās architecture for implementing construction and deconstruction waste (CDW) management strategies, which ensures that the model is flexible and that different parts of the model can work together to access and exchange data reliably and accurately. The four-layered modelās architecture encompasses comprehensive information and interactions regarding the integration of data schemas between BIM, Google Maps, and CE principles while residing in Autodesk Revit as BIM tool, consisting of: i) input data and information layer; ii) criteria required to initiate and execute analysis; iii) various analysis to be performed directly or via a new plug-in in BIM environment and; iv) output layer consisting of result from the integrated model in the form of an analysis, evaluation or cost reports to support decision making, as shown in Figure 1.
Moreover, the model architecture is supported by data flow that focuses on representing how the data is transmitted through the different parts of the layers during the implementation of the integrated model. The process flow demonstrates how data enters and exists out of the model and the resulting output generated by the integrated model, as illustrated in Figure 2. The data flow consists of a set of processes that convert input data into output data, connected by flows that indicate how the data is transmitted between processes. Each data and process in the model represents an operation that
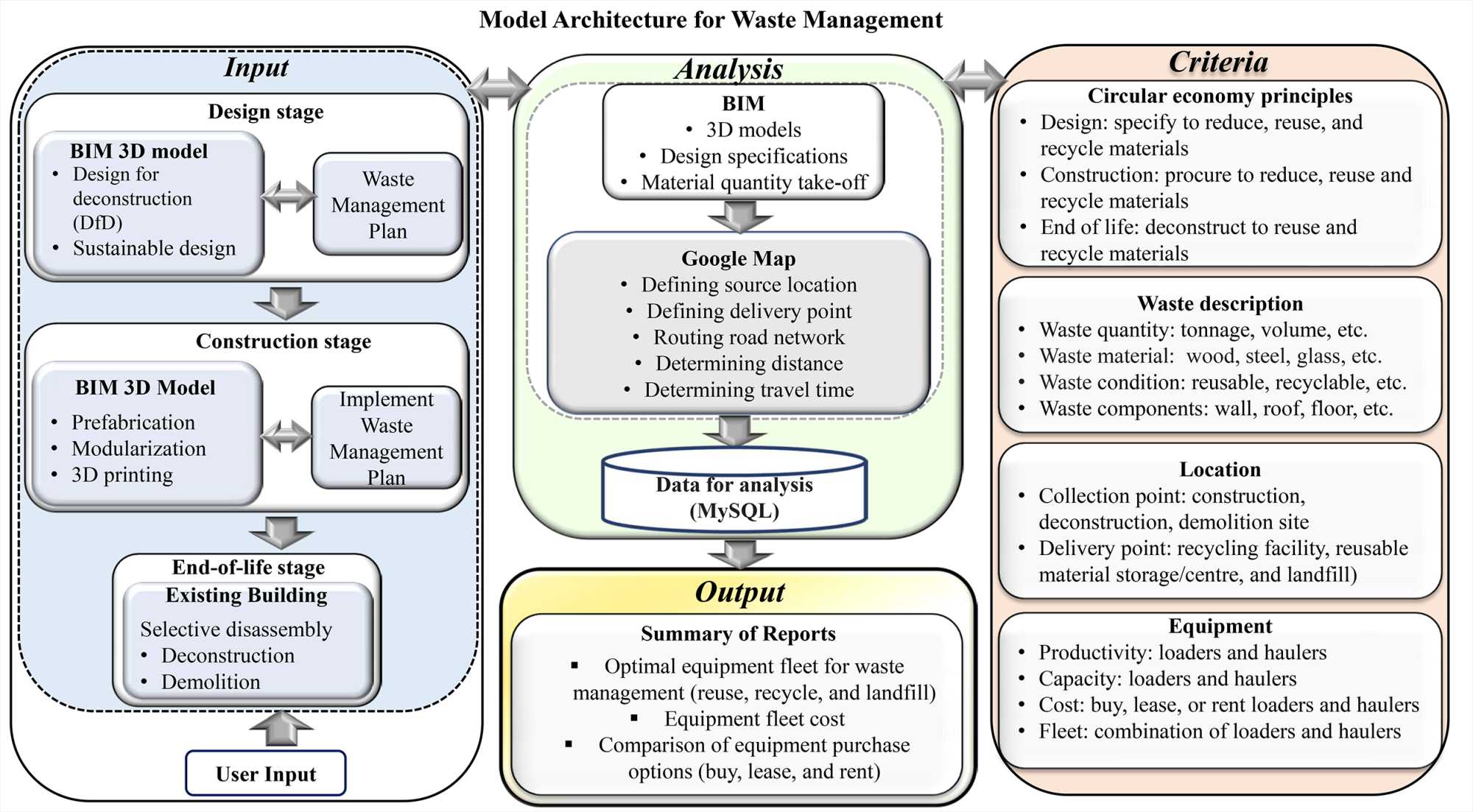
Figure1.Modelās architecture of BIM-Google Maps-CE for CDW management.
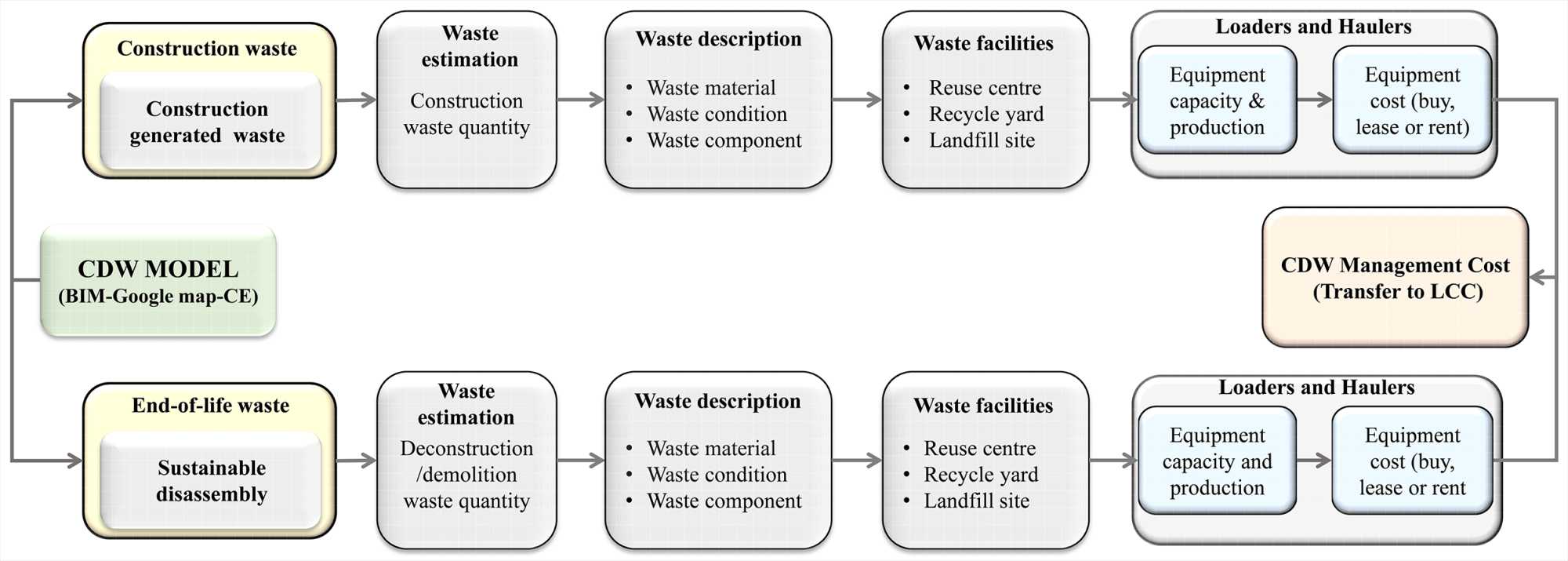
Figure 2.Modelās data flow for implementing CDW management.
requires one or more inputs and produces one or more outputs. Thus, to determine the required equipment, its production rate and associated costs are calculated by a customized plug-in that has been developed for that purpose in Autodesk Revit integrated Google Maps services for a combined query utilizing their analysis capabilities. The plug-in uses a combination of data stored in MySQL database, such as location, attributes, quantity, and corresponding features, and data associated with the CE concept, such as reuse and recycling content of a material, to run and complete all the necessary calculations and analyses.
The development methodology follows a BIM-leads approach linking various tools and data to develop the BIM-Google Maps-CE integrated model, which will be implemented through five sequential phases, as shown in Figure 3.
Phase 1 focuses on the creation of a databasefor organizing and storing information about materials and components associated with the three construction methods as an external database with all necessary data for appropriate retrieval, modification, and update. Information about sustainable materials are collected, stored, and used to create 3D new sustainable design families. The storage of the newly created families in BIM tool (i.e., Autodesk Revit) with a file extension of (.rfa) or Revit project (.rvt) file formats (such as door, window, wall, floor, ceiling, roof, etc.) and their associated parameters (such as keynotes, assembly code, specification, and description) for the three abovementioned construction methods is another significant focus of this study. The three databases are integrated with BIM tool through an automated link to aid in carefully evaluating and selecting the material. Hence, developing a separate external database for each design enables the associated families to load upon opening BIM tool and making the components accessible directly from the database during the design process.
Phase 2 emphases on creating BIM 3D design model(s) that receive their information from the database to enhance the design, construction, and deconstruction processes by using BIM tool (Autodesk Revit). Three identical models will be created, separately, based on the three construction methods. The modular design will be based on the design for deconstruction (DfD) approach and will be constructed in the form of prefabricated components, the 3D concrete printing design will be based on the specification of the selected printer and its compatible mortar paste, while the conventional design follows the traditional method of buildings by using wood-frame structure. In addition, BIM tool will be customized by modifying its functionality to suit the flexibility requirements of the proposed model in providing additional detailed information, such as construction specifications, quantity, waste percentage, and material bulk density, to enhance material traceability and waste management analysis. Furthermore, CDW attributes will be created in BIM tool (Autodesk Revit 2020) by selecting Project Parameters in the Manage tab to add project properties to both the āProject parameterā and āShared parameter,ā as shown in Figure 4. The additional attributes are essential because the associated parameters of the family are required to identify the waste component of individual material during the quantification of waste. For example, a new material waste attribute called āBulk densityā in the existing āConstructionā group parameter is added, as illustrated in Figure 4. The figure also shows numerous options for expressing the parameter type in Autodesk Revit, such as number (volume, length, area, distance, rotation angle, pending, time, speed, currency, URL, and material). The parameter selected is āmaterialā to express waste attributes of walls and windows and kg/m3 was chosen as the unit to express the values, as shown in Figure 4.
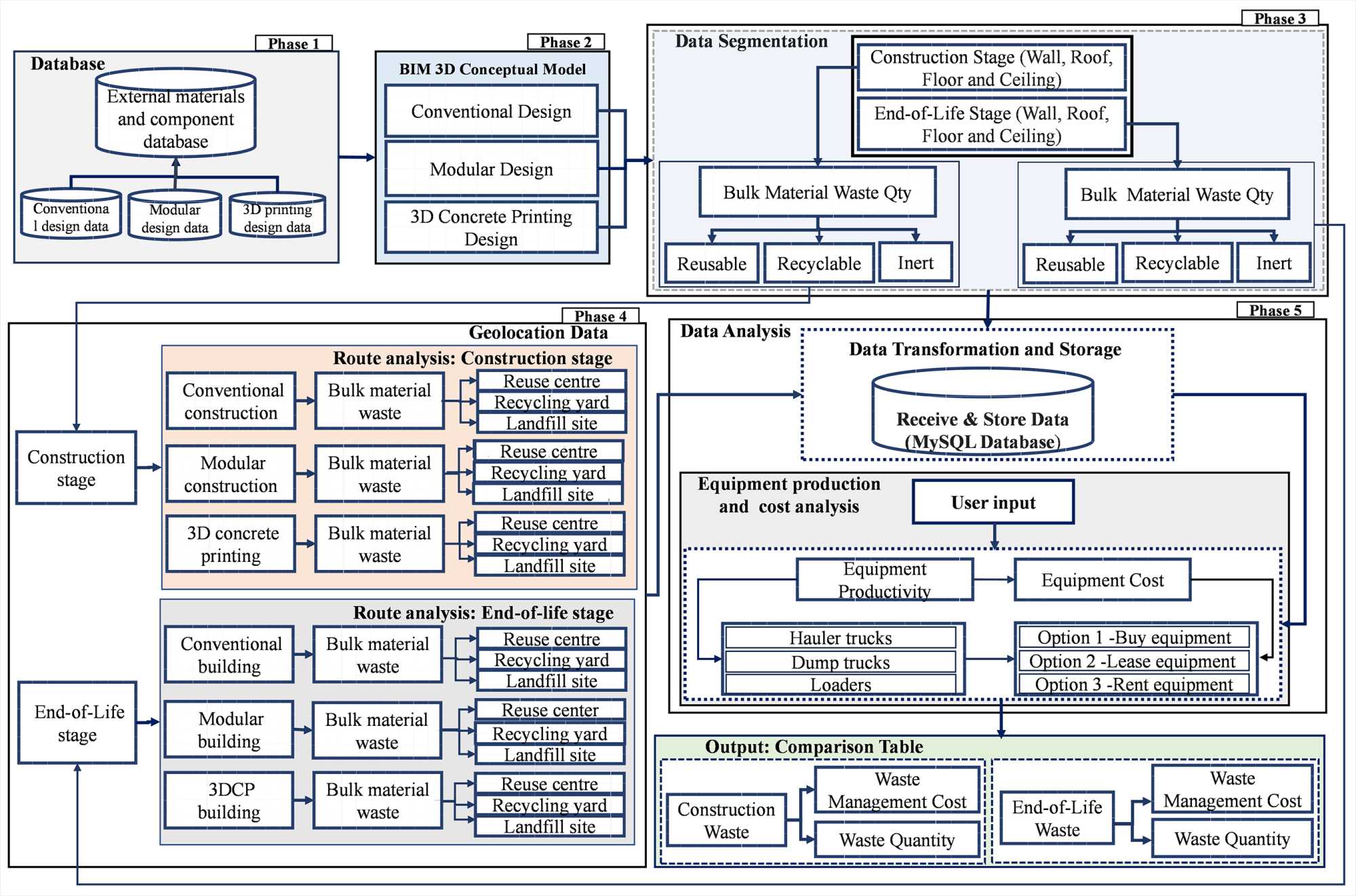
Figure 3.Modelās components and phases.
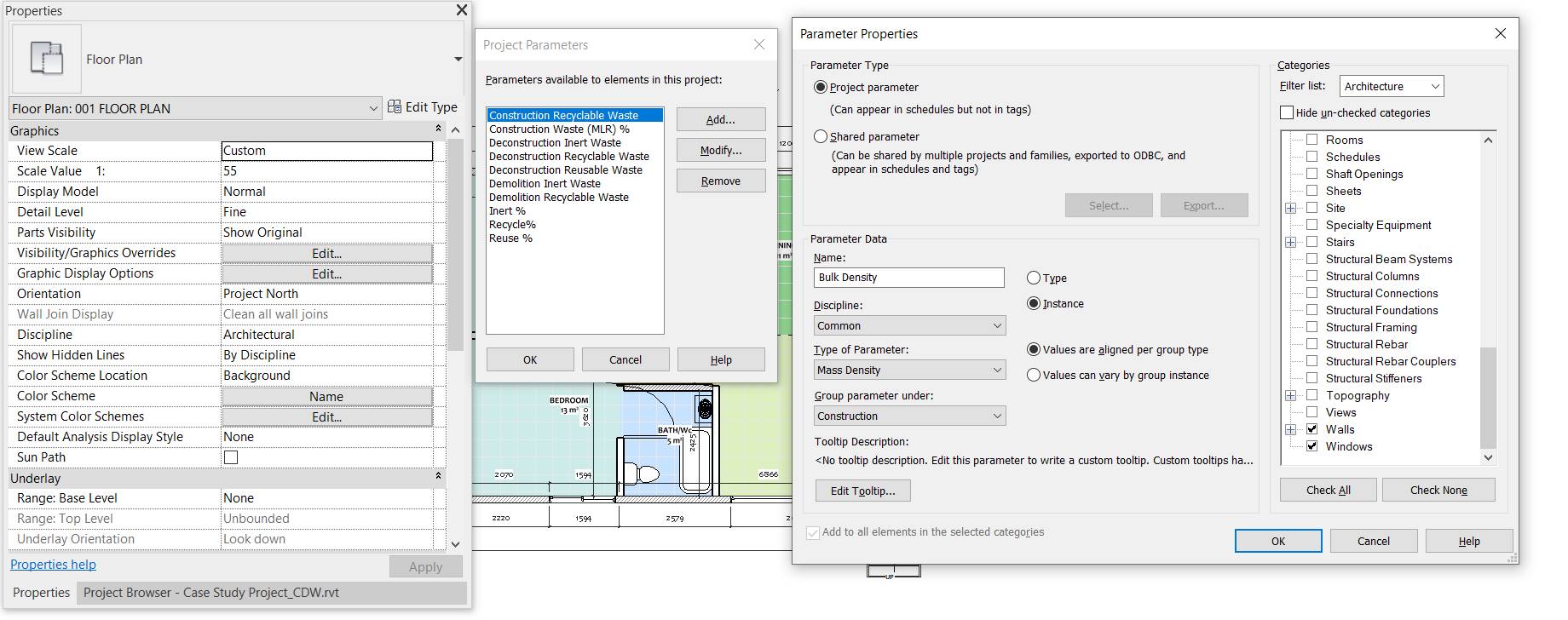
Figure 4.Process of creating waste attributes in BIM tool (Autodesk Revit).
Phase 3 involves the development of a data segmentation to structure waste material into an exclusive data format to aid in an adequate evaluation and efficient decision-making. The process uses the conceptual design model, formally created, of the three design methods (conventional, modular and 3D concrete printing) to formulate various data segregants for easy evaluation. Firstly, into two lifecycle stages: construction and end-of-life; secondly, the bulk quantity of material waste for each lifecycle stage; and thirdly, into three forms of measurable waste (i.e., reusable, recyclable and inert) based on the circular economy concept. This study uses a BIM-based quantity takeoff (QTO) to estimate the wasted materials following the mass balance principle at the construction stage and the total material incorporated in the existing building for the end-of-life stage. The waste generated during the construction stage is considered as the fraction of materials purchased, less the quantity of materials needed to construct a building, by using Equation (1), while the end-of-life waste accounts for all the materials permanently incorporated into a building. After extracting the materialsā quantity takeoff from Autodesk Revit and exporting it to Microsoft Excel, the quantities of waste are further sorted and structured based on the material type, life cycle stage, and the condition of the generated waste.
Construction waste=āmaterial purchasedāāneeded materialConstruction waste=āmaterial purchasedāāneeded material(1)
Phase 4 focuses on integrating GoopleMapās tool with BIM tool (Autodesk Revit) to provide the necessary information, such as transportation route, distance, and facilitiesā location, by defining interconnected lines (edges) and intersections (junctions) representing a path for the travel from one location to another. The dynamic mapping capabilities of Google Maps provide a robust platform for conducting in-depth analyses, including extensive and up-to-date geographic data, making it a valuable tool for spatial analysis, route optimization, and location-based insights. In this study, Google Maps integrated with BIM tool is used to compute and determine the optimal routes from one location to another for a given network assigned by users in identifying the nearest, shortest, fastest or safest route between various locations. Thereby overlay accurate 3D BIM models onto real-world geographic locations, enhancing spatial awareness and facilitating a better decision-making throughout the project lifecycle. Three different locations have been identified in this analysis, which are: location for waste generation (construction/deconstruction/demolition site); location for off-site waste sorting (bulk material waste sorting); location for waste delivery (material reuse center, recycling facility, storage or landfill) for both construction and end-of-life waste estimation process, as shown in Figure 5.
Phase 5 concentrates on data analysis by using inputs from the various modelās phases. The initial phase of the analysis involves the creation of a MySQL-based database management system. This system is designed to efficiently store the substantial data produced through phases 3 and 4, which will be structured logically to provide versatility within the programming environment to facilitate the automation of data transmission. Hence, MySQL database is the source that hosts detailed data about equipment production analysis and cost estimating for CDW evaluation. Additionally, the scope of work and the equipment requirements are the two primary considerations for the waste equipment analysis since the scope of work helps in determining the type and capacity of the waste handling equipment. Thus, the analysis for waste handling equipment will be carried out using specifications retrieved from Caterpillar Performance Handbook . The primary objective of the analysis is to ascertain the production capacity, and the number of individual equipment required. This study considered the following waste handling equipment for the evaluation: dump trucks for transporting waste from construction sites to bulk waste sorting sites; loaders and haulers for loading and hauling from bulk waste sorting sites to recycling, reuse centers and landfill sites based on the quantity of waste, equipment capacity, specifications, job description, and location. A waste-handling wheel loader will be used as the loading equipment since they are equipped with

Figure 5.Route definition for network analysis.
the features and protection required in a demanding waste-handling environment, while the loader and truck production rate will be calculated in weight per hour since construction, demolition and deconstruction waste materials are considered. The steps to determine the various associated factors with the analysis will be adopted from the literature.
Furthermore, the equipment cost analysis uses the procedure employed by the construction industry to estimate the hourly operating cost of equipment, such as fuel consumption, tire life, etc. Equipment owning costs will be estimated as follows: 1) depreciation using the straight-line method; 2) investment cost using the value of the average investment over the life of the equipment; 3) insurance, covering for fire, theft, accident, and liability; 4) ownership tax and licenses for the equipment; and 5) cost of rent and maintenance for equipment storage. All the listed elements of owning cost may be calculated on an annual or hourly basis costs, however, the total owning cost will be expressed as an hourly cost in this study. Operating costs will be incurred while the equipment is in use, hence, costs may vary depending on the equipment usage and job operating conditions. The major elements of the operating cost will include: fuel cost; service cost; repair cost; tire cost; cost of special items; operatorsā wages and logistic cost, while the associated cost will be retrieved from historical data or equipment manufacturer recommendations such as Caterpillar Performance Handbook [43]. The equipmentās detailed estimation will include three cost options (buy, lease and rent), offering users a range of choices and flexibility for efficient decision-making. The evaluation will be applied to the three designs and construction methods (conventional, modular and 3D concrete printing) at the construction and end-of-life stages for the bulk of material waste and the associated forms of waste recycling, reuse and inert to determine the optimal fleet of equipment for the CDW management.
Model Implementation
The model implementation is achieved by customizing and extending the capabilities of the existing APIs of BIM tool (Autodesk Revit) using the software development kits that serve as the building blocks for software applications. These tools enabled the authors to write code that added new functionality to comply with the needs of the BIM-integrated model. Accordingly, the functionality of the integrated model is implemented by developing a plug-in in BIM tool using its API, Visual Studio and C# programming language to link the Google Maps tool and other associated data processes as described in the development methodology. The complete integration of the five phases is achieved by using a newly created plug-in to facilitate all the processes involved in quantifying the wasted material, selecting the equipment for waste handling and the cost associated with the waste loading and hauling at the various stages of a project through an interactive user interface (UI). Users need to access the complete user interface by clicking on the COMOTH_CE tab, which is a newly created plug-in in the Autodesk Revit, to start the waste planning and evaluation processes for their design, as shown in Figure 6. Upon clicking on the tab, the first page opens with two prompts, continue and exit, followed by the home page, which contains the basic information for the design platform, such as two options for the number of floors and three associated with the different construction methods, about, exist and reset. The āAboutā helps users to familiarize themselves with the user interface by providing a general introduction and tutorial concerning the plug-in and how to use the model to achieve optimal results. The integrated model is developed to provide several options with two main design alternatives (1 – 3 floors and above three floors building) and implemented to evaluate and plan the construction demolition and deconstruction waste (CDW) management strategies for the three construction methods, namely conventional, modular and 3D concrete printing for the construction and end-of-life stages, except for the 3D concrete printing method, which is only applied for a maximum of three floors buildings.The model is developed to quantify the wasted materials for four waste categories; bulk, recyclable, landfill, and reusable waste material, for each construction method, as shown in Figure 6. For each of the mentioned waste category, the plug-in implements three analyses to complete the evaluation of the CDW management process as follows: a) quantifies the associated wasted materials; b) calculates the productivity of the
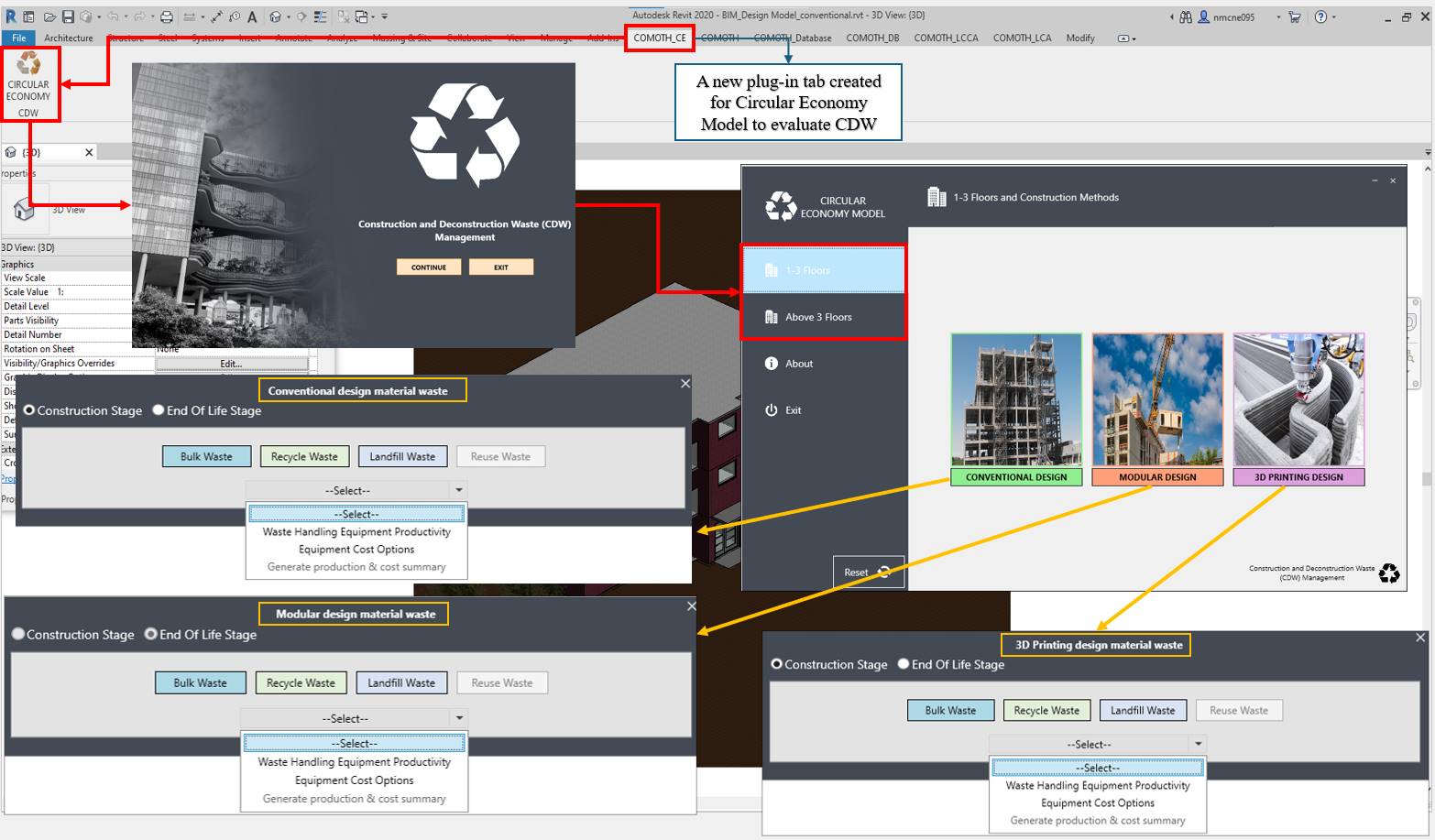
Figure 6. Snapshot of the plug-in layout showing design options.
equipment required to handle wasted material; and c) estimates the costs associated with the waste handling equipment. The productivity and cost of equipment are estimated based on the userās requirement by selecting the form of waste and then clicking on the select dropdown, as shown in Figure 6. Moreover, the model requires users to provide some necessary input to suit their design needs, such as the name or address of the waste facilities for the travel distance to calculate the equipment productivity and fuel price to calculate the equipment cost. By selecting the bulk waste, users can estimate the productivity of a dump truck and the associated cost options of buy, lease or rent; the recycle reuse and landfill options also provide users with the hauler truck and loader productivity and their related cost options(s). One of the main advantages of the implemented model is that it provides designers with a more precise calculation when finalizing the evaluation and cost estimation for the equipment selection. The integrated model is developed and implemented to use a built-in algorithm to select the waste handling equipment and the cost associated with loading and hauling the waste of construction and end-of-life stages based on three options: buy, lease, or rent the equipment. The implementation process is applicable to conventional, modular and 3D printing designs in this study. However, the type of design must select its construction method to initiate and complete CDW management evaluation and analysis.
Model Testing
Testing the model is challenging because the authors could not find data about real project to compare the modelās outcome to the ones of the existing project that used modular and 3D concrete printing. The developed model is tested to verify its capability and workability in terms of the input, relevant criteria, subsequent analysis, and generated output through a real three-floor residential building by creating three identical 3D BIM models of the project, which is currently under design in Ottawa, Ontario, Canada. Autodesk RevitĀ© as BIM tool is selected to create the buildingās 3D design models using the design families stored in the external database, which are retrieved through a plug-in located at the top taskbar of Autodesk Revit and named DB. The design components, such as the floor, wall, ceiling and roof, were customized with additional parameters to define and account for the recyclable, reusable and inert waste contained in the materials of those elements at the construction and end-of-life stages based on the information retrieved from the related literature. However, all substructural elements and associated materials for works below the floor slab were excluded, as the study assumes that all three designs have a similar foundation.
Once the design model is created, designers can evaluate the construction and deconstruction quantities of the wasted material. As mentioned, the integrated model uses three types of analyses following various steps, as shown in Figure 7, to execute and complete the required evaluation for the selection of optimal equipment for handling CDW waste based on the form of wasted material.
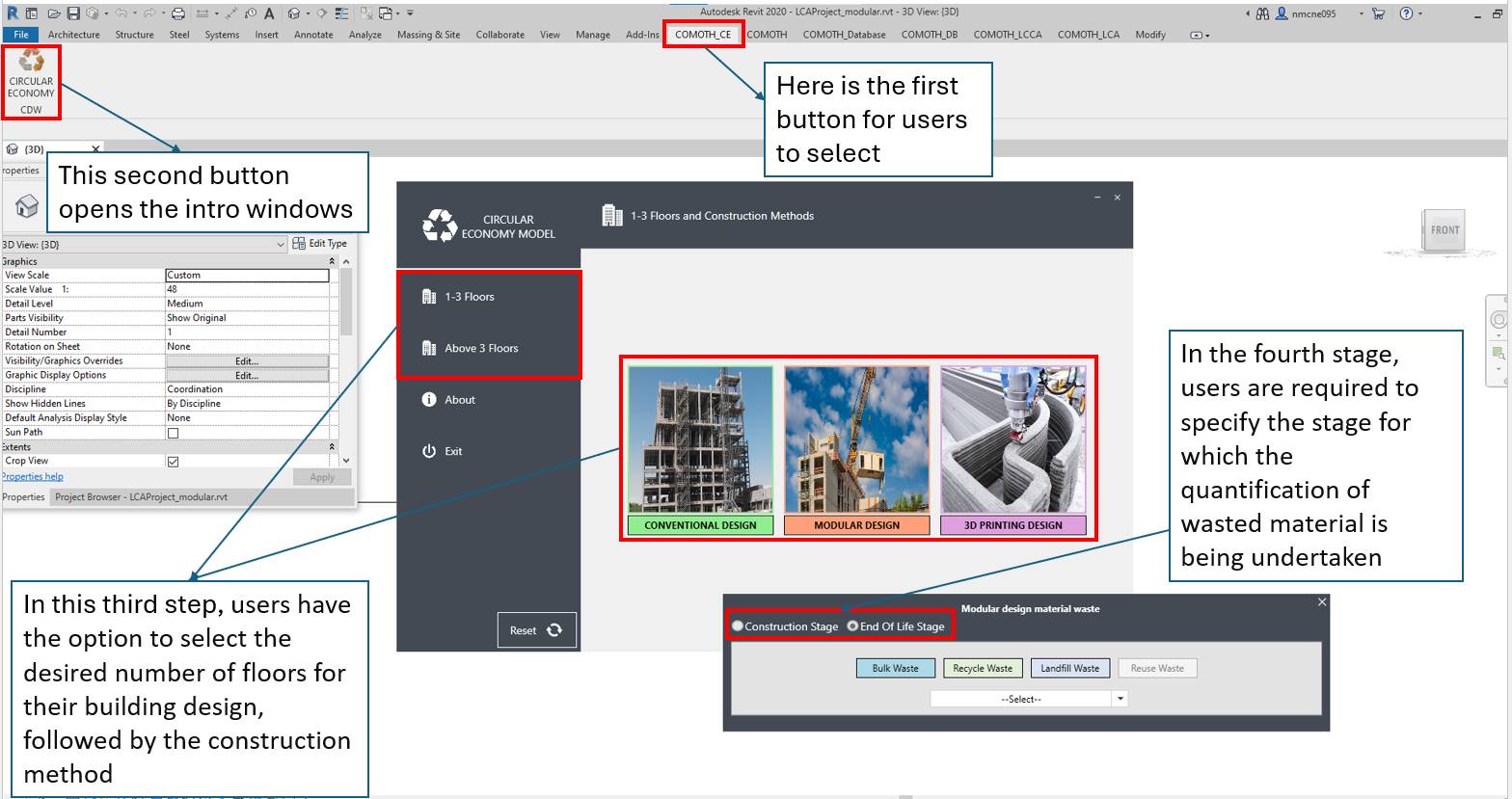
Figure 7.Various steps for the Modelās analysis.
In the first step, the designer starts by clicking on the COMOTH_CE plug-in tab and the circular economy push button, which opens the user interfaces, ready to commence the analysis, as shown in Figure 7. In this case, users will be required to make a selection from the two options for the number of floors (1 – 3 floors and above three floors); select the construction methods (conventional, modular and 3D concrete printing); and choose the lifecycle stage (construction and end of life), then the form of waste and the type of analysis from a dropdown menu. By selecting the type of analysis, the model automatically generates the quantities of the wasted material associated with the selected form of waste and populates the appropriate cells for material qty (cy) and material qty (lb), as shown in Figure 8. It is worth mentioning that in this model, the same processing steps are applicable for measuring all forms of wasted materials.
Next, the user is required to calculate the equipmentās productivity and explore the associated cost options. Within a dropdown menu there are two options for the types of analysis and a summary. The initial selection from the dropdown pertains to the productivity of the waste handling equipment, which initiates the opening of a new window for user input, as shown in Figure 9. Subsequently, the user proceeds with the process by clicking on the map icon within the distance cell. This action launches the Google Maps application on a new screen, facilitating the plan of the select locations of the collection and delivery facilities for the generated waste material. In this study, the Google Maps application has been customized to enable users to input a starting and ending locations and then perform a search. After users input the required information, the model will initiate the search and compute the distances between identified
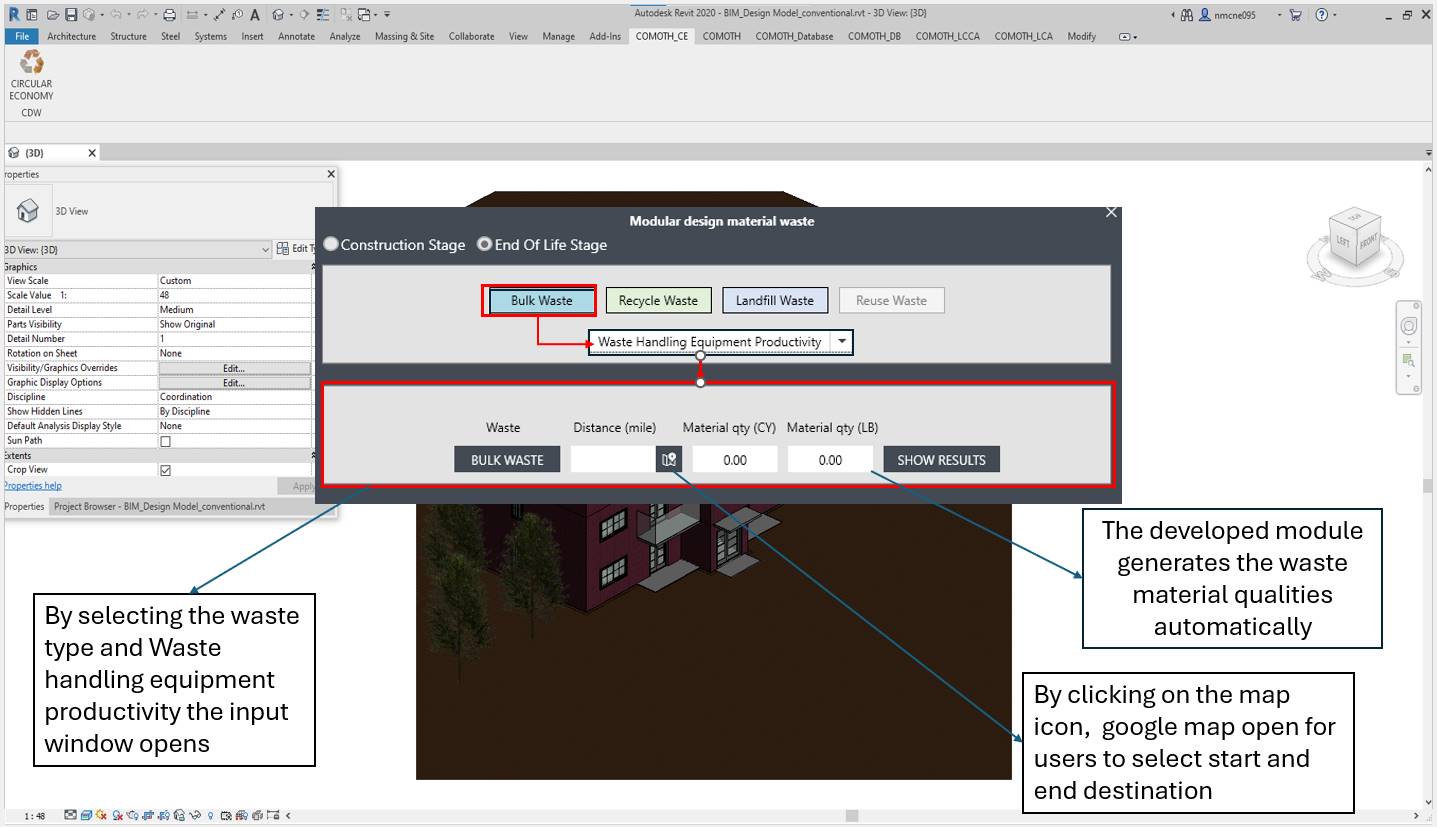
Figure 8.Process of generating wasted material quantity.
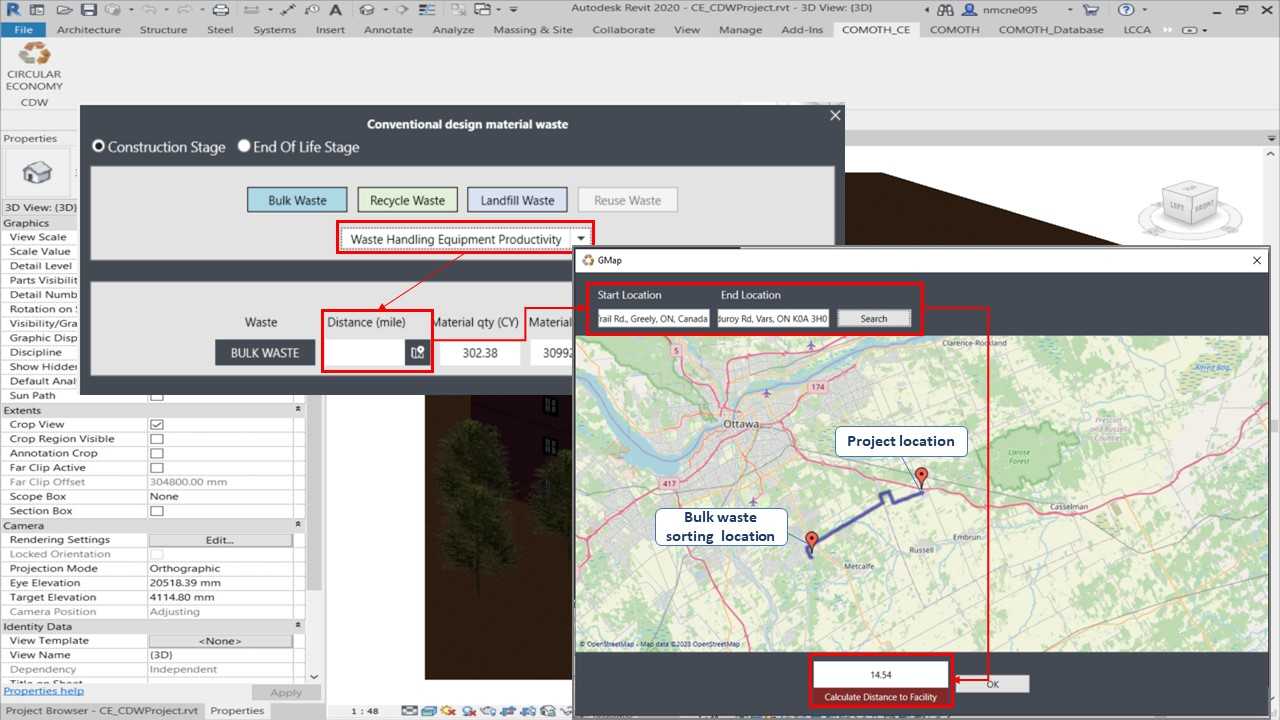
Figure 9.User input for selecting distance between facilities in BIM-Google Maps.
facilities to ascertain the closest, fastest, or safest route among various locations. This information is then integrated into the calculation of travel time to determine equipment production rates. Figure 9 also shows an example of calculating the distance between the construction site and the sorting facility for bulk waste material, which accounts for 14.54 miles. Users can employ the same steps to calculate distances between any waste material pickup location and its corresponding delivery point within the scope of this model, whether it is a recycling yard, reuse center, or landfill site. Next, the modelās algorithm leverages the entire set of customized parameters, including a database, to compute the productivity of waste handling equipment, as defined in phase 5. The computation incorporates user-provided input data, specifically the travel distance, to finely calibrate the modelās requirements, thereby generating a more reliable estimation. Afterwards, the model undertakes all requisite calculations and evaluations in the background and then furnishes users with production rate outcomes for diverse equipment, as illustrated in Figure 10. Although bulk waste is used in the illustration, the same process is applied to quantify other waste materials such as recycling, reuse and landfill.
Similarly, the user estimates the costs associated with the waste handling equipment by selecting āEquipment Cost Optionsā from the dropdown menu, which then opens a secondary selection menu containing a list of associated cost options: buy, lease, and rent options. After selecting from this menu, another window emerges, allowing the user to input cost-related information. The required user input for finalizing the equipment cost modelling in this study is fuel cost expressed in dollars/gallon. Once the necessary data is provided, the model retrieves other essential and supporting information from the database. It then proceeds to perform all the required calculations and evaluations in the backend, ultimately providing users with the equipment cost, as demonstrated in Figure 11. It is worth noting that while the illustration uses the ābuyā costs, the same procedure applies to estimating other options, such as lease and rent.
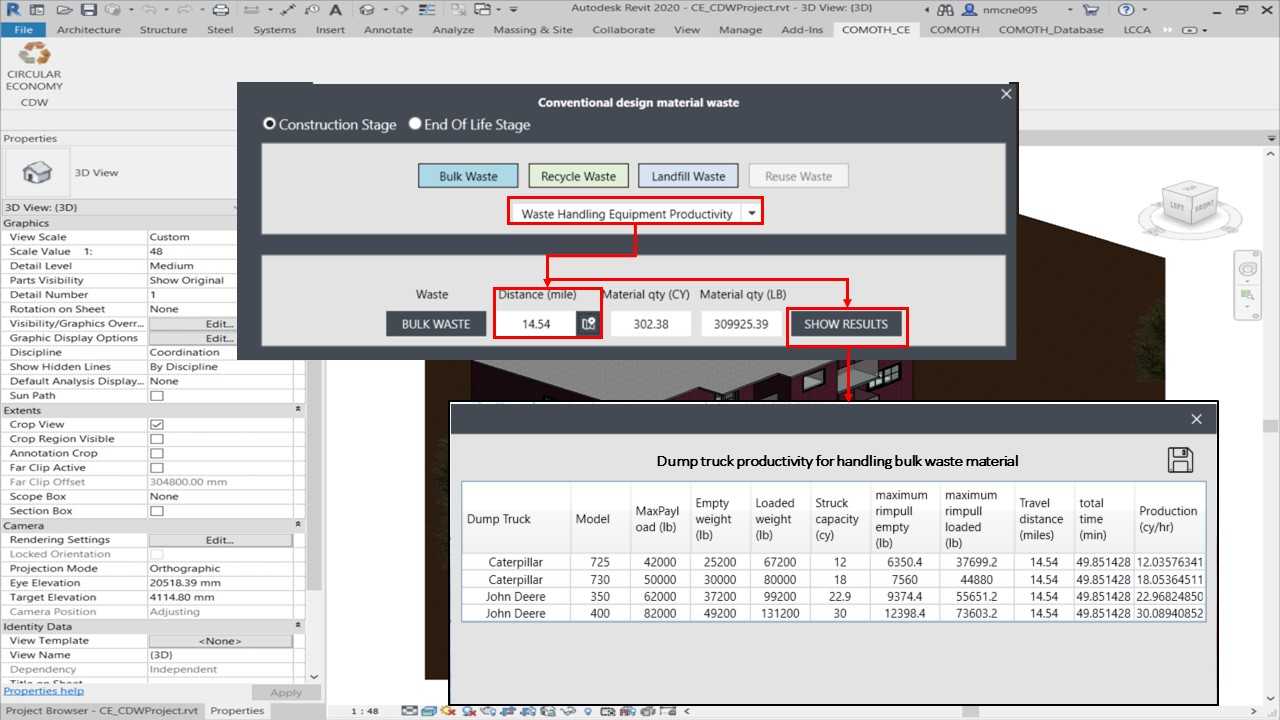
Figure 10.Result of the waste handling equipment productivity.
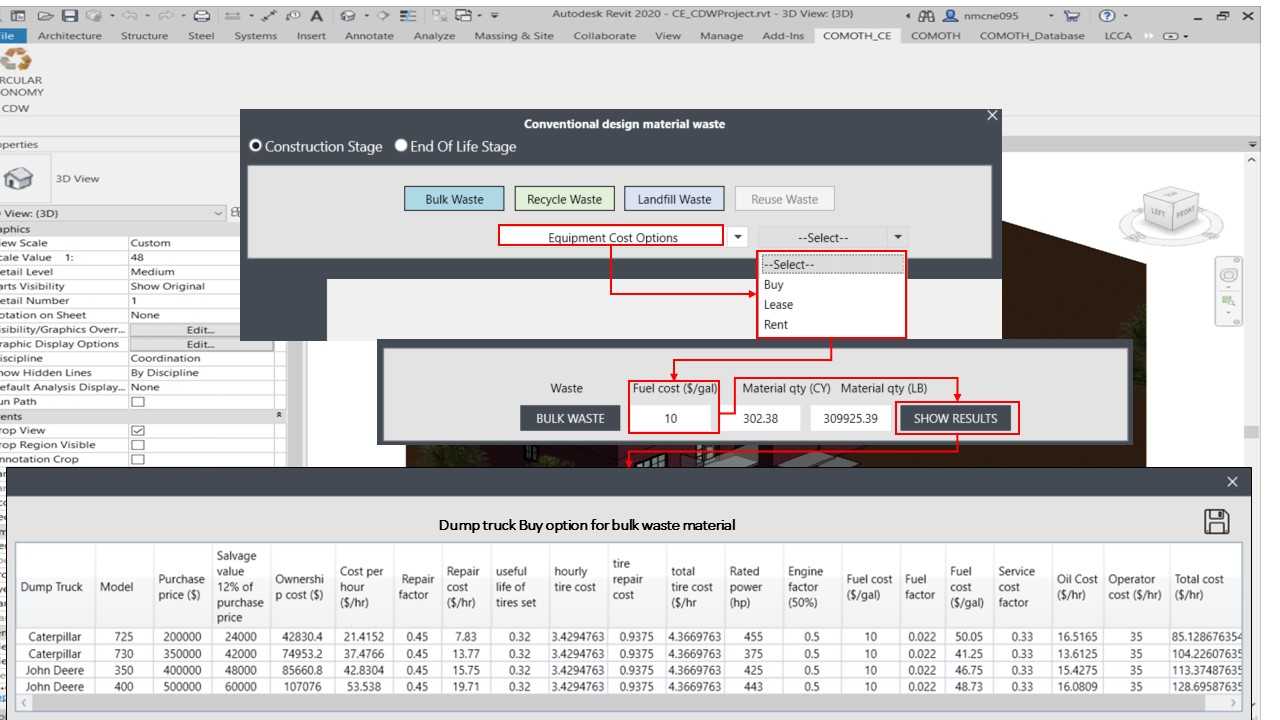
Figure 11.Result of the waste handling equipment cost (buy option).

Figure 12.Summary of waste handling equipment report.
Upon completing the necessary analysis in the dropdown menu, users can generate the analysis summary by clicking the final button labelled āGenerated production and cost summary,ā as depicted in Figure 12. This summary allows the user to make a side-by-side comparison of the different equipment options in terms of production rates and costs. Consequently, the user can confidently select the most efficient and cost-effective choice. It should be emphasized that the process of estimating production rates and costs for the waste management equipment using the developed model is applicable to conventional, modular, and 3D concrete printing construction methods. Therefore, users must choose their construction method at the start of the evaluation to obtain relevant results.
Discussion
6.1. Model Evaluation and Comparative Analysis
The automated model developed in this study integrates tools and data to assist designers in the evaluation and planning of construction and deconstruction waste (CDW) management strategies by quantifying waste at various lifecycle stages based on the concepts of circular economy, including waste handling equipment and the cost associated with loading and hauling the waste of a building projectin an effort to enhance the sustainability of buildings from design to end-of-life stages. The design process incorporates the Design for Deconstruction (DfD) concept to integrate construction circularity into sustainability. The construction process employs sustainable construction methods capable of standardizing, prefabricating, and 3D printing building components with concrete. Selective disassembly is employed at the end of its life to manage deconstruction waste effectively.
Therefore, by comparing the developed model with earlier models found in the existing literature that integrate BIM for assessing waste management during the design phase, one can better understand the presented model. This understanding encompasses the following four key aspects: Firstly, its capacity to incorporate various construction methods (such as conventional, modular, and 3D concrete printing). Secondly, its effectiveness in implementing waste management strategies from the design phase through to the end-of-life phases. Thirdly, its ability to measure and manage four forms of measurable waste based on the circular economy concept: bulk, reusable, recyclable, and inert materials. Fourthly, its capability to quantify the production rate and associated cost options for waste handling equipment. Those four aspects collectively contribute to the modelās strengths and completeness, which are essential considerations for its application in waste management within the construction industry.
Despite the existing body of knowledge and successful models in the integration of Building Information Modeling (BIM) with waste management , many of these models predominantly rely on conventional design and on-site construction methodologies and do not possess the four described attributes of the developed model, for instance, the model introduced in leverages a BIM-integrated system to extract material and volume data for the purpose of estimating and planning recycling and waste reuse, encompassing the prediction of requirements for pickup trucks and waste disposal costs across various waste facilities. Al-Saggaf and Jrade proposed a model that streamlines waste quantity estimations by factoring in travel distances between the construction site, storage areas, landfills, and associated time considerations, including the computation of the necessary number of trucks for waste loading and transportation between multiple sites.
Furthermore, proposed the BIM circular economy model that primarily focuses on materials analysis of the structural components of buildings based on on-site conventional construction. The conventional construction method has been widely recognized as a substantial impediment to the integration of Circular Economy (CE) principles within the Architecture, Engineering, and Construction (AEC) industry. This is attributed to its monolithic characteristics, architectural limitations, lack of standardized metrics, and the nascent development of closed-loop stakeholder engagement within the design and construction processes. Conversely, the utilization of modular off-site prefabrication and 3D concrete printing in construction, as demonstrated in this study, is acknowledged for their cleaner production attributes, which are fundamental in the context of industrialized construction (often referred to as Construction 4.0). These methods have been shown to play an important role in the evaluation and management of construction and deconstruction waste (CDW). Additionally, the integrated BIM model encompassing these innovative construction approaches holds paramount significance in advancing sustainability within the construction industry.
6.2. Contributions and Challenges of the Implemented Model
The primary qualities of the developed model lie in its capacity to use circular economy principles integrated with BIM to assess material waste management strategies pertaining to both the construction and end-of-life phases of a building, particularly in the context of modular, 3D concrete printing, and conventional construction methods. The developed model offers valuable insights by accurately calculating the production rate of waste equipment and presenting different cost options (including buy, lease, and rent) for dumpers, loaders, and haulers. These capabilities significantly contribute to informed decision-making during the conceptual design phase, thereby facilitating the pursuit of sustainability objectives within the construction industry.
Thus, one of the notable contributions of this study lies in the capacity of the developed model to furnish designers with a versatile tool encompassing comprehensive data for the planning and evaluation of various management strategies concerning construction and deconstruction waste (CDW) during the design phase. The model presents a range of options, including two design alternatives (one to three-floor and above three-floor designs); three construction method choices (conventional, modular, and 3D concrete printing); various waste handling equipment specifications (loaders, dumpers, and haulers production rate); three equipment cost alternatives (buy, lease, and rental); and four waste disposal methods (bulk, recycling, reuse, and landfill) within two distinct lifecycle stages (construction and end-of-life). These provisions enhance the efficacy of CDW management.
Previous studies have emphasized the potential of recycling and reusing materials and components in construction to target approximately three billion tons of raw materials on a global scale, representing significant economic benefits. This equates to approximately 40% to 50% of the total economic output of the global economy. Hence, a second significant contribution of this study is its expansion of existing knowledge by incorporating additional dimensions of economic sustainability. This is especially pertinent because the existing literature indicates a bias towards environmental sustainability in most sustainability assessments, with limited consideration for economic and social sustainability aspects. Consequently, the developed model possesses the capability to quantify the material waste, evaluate the waste handling equipment rates, and estimate the associated costs related to loading and hauling the waste to various facilities. This equipment estimated cost translates into a lifecycle cost of a building project, particularly in the context of sustainability assessments, and it is often neglected or approximated due to the absence of existing models for precise estimation.
The developed model, additionally, contributes to architecture, engineering, and construction (AEC) practice by providing a measurable implementation and application of circular economy principles that enhance the sustainability of building projects. The novelty of this study lies in the technical contribution of developing an integrated model that links Building Information Modeling (BIM), Google Maps, and Circular Economy (CE) concepts. The primary focus centers on reducing, reusing, and recycling construction materials within building projects and is achieved through developing a unique plug-in that extends the functionality of BIM tool and is implemented in an Autodesk Revit design environment.
Notwithstanding the various advantages of the model outlined above, it is imperative to acknowledge a limitation in its current iteration. The developed model is presently restricted to selecting specific types of construction equipment, namely loaders, dumpers, and haulers. This constraint restricts users from choosing from within the predetermined equipment options the model provides. Furthermore, the lack of standardized metrics and policies for circular economy practices in the construction industry can make the development of BIM-CE models in the existing construction workflows a big challenge. Each project might interpret or apply the CE principles in different ways, which will lead to inconsistencies in CDW management and hindering the sustainability goals of construction. Therefore, effective development of BIM-CE models requires active participation from all stakeholders, such as designers, contractors, clients, and policymakers, because any opposition from any of these groups could obstruct the integration of these models into the current construction workflows.
However, it is noteworthy that this research holds significant potential for further improvement, implementation, and validation. Therefore, the future expansions of this study will concentrate on the development and seamless integration of a comprehensive database capable of storing detailed information pertaining to a wide spectrum of construction equipment, since the effectiveness of these models is limited by the accuracy, quality and completeness of the entered data, using inaccurate data can lead to making inefficient decisions, which negatively influence the adopted circular economy strategies. This extended functionality will encompass data such as production rates, specifications, and associated cost parameters. Incorporating this enhancement will substantially augment the modelās capacity to facilitate decision-making in planning and managing construction material waste. Furthermore, the BIM 3D design model(s) utilized for assessing the modelās feasibility and workability excluded materials for the substructural building elements. This omission was deliberate as these elements were deemed identical across the three design models under investigation (i.e., conventional, modular, and 3D concrete printing).
Finally, this study possesses substantial potential for subsequent design, analysis, implementation, testing and validation phases. Consequently, the authors are working on enhancing the model with the focus on establishing and expanding a comprehensive database encompassing loader and hauler equipment alongside a broader array of waste handling and construction equipment. This extended database should include intricate specifications and cost parameters integrated with the evolving model to facilitate a more comprehensive and detailed analysis incorporating CE and BIM.
Conclusions
This paper outlined the development of a model that harmoniously integrates BIM, Google Maps, and CE principles to accomplish its primary aim of assisting designers in enhancing construction sustainability and minimizing lifecycle waste across various construction methods, including conventional, modular, and 3D concrete printing. The study primarily focuses on the conceptual design phase, a crucial stage where informed decisions regarding project costs and benefits rely on access to vital information. The modelās core objective is to provide designers with a streamlined approach that seamlessly incorporates waste management strategies into the conceptual design process. It achieves this by leveraging circular economy principles that connect the strengths of BIM tools, Google Maps, and other relevant data sources. This comprehensive integration significantly elevates sustainability performance and ensures reliable outcomes throughout the planning and design phases for the three construction methods mentioned earlier.
The development of the integrated model involved a process of customization and extension of BIM and Google Maps tool functionalities through the utilization of software development kits (SDK). This allowed authors to introduce new features and functionality that seamlessly integrated Google Maps tool and other data sources throughout the five phases of the integration process.
One crucial aspect of this modelās development was the customization of BIM tool, which was achieved through an automated process involving the creation of new plug-ins, which, in turn, embraced elements from the Industrialized Production layer of Construction 4.0. Specifically, this integration encompassed aspects such as modular prefabrication and 3D printing methodologies. Hence, designers will seamlessly integrate this plug-in into the early stages of designing sustainable buildings, ensuring efficiency and cost-effectiveness.
The requirements for implementation of the developed model were first established through a comprehensive literature review and data collection to ascertain the actual needs, gaps, and expectations of the integration for sustainable design related to CDW when selecting a design of a construction method. Then, the conceptual integration process uses gap analysis to identify effective solutions, followed by full development of the BIM intergraded model, which holds the proposed solutions for the identified gaps through its five phases. This process has been identified as a potential solution to achieve sustainability in the building construction industry through the design, construction, and deconstruction processes.